Het boorproces !
Een aantal foto's op deze pagina kunnen worden vergroot door er op te KLIKKEN !
Na het uitgevoerde seismisch - onderzoek, waaruit het vermoeden bestaat, dat er zich in de diepe ondergrond aardgas aanwezig zou kunnen zijn,
is er maar 1 mogelijkheid dat vast te stellen. Dat is het verrichten van een proefboring.
De boortoren van de NAM in 1959, op het land van boer Boon. Dit was de boring Slochteren 1.
De ontdekking van het gasveld Groningen.
Deze toren werd destijds voor een groot deel opgebouwd in handkracht.
Later is de put dichtgemaakt en verlaten, i.v.m. de aanleg van de A7 Groningen - Bad Nieuweschans.
Om zekerheid te krijgen of er in de diepe aardlagen, het Rotliegend-zandsteen aardgas aanwezig is, zal in het gebied een boorlocatie worden aangelegd voor een proefboring.
Dit gebeurde in 1959 bij het Groningse dorp Kolham (het toenmalige gemeente Slochteren).
Alvorens met het boren van de put kan worden, wordt vervolgens een ruime stalen buis de grond ingeheid, tot 30 m. diepte ter bescherming van grondwater. Hierna wordt een betonnen putkelder om het bovenste deel van de buis aangebracht. In deze putkelder staat tijdens het boren een grote veilgheidsafsluiter (Blowoutpreventer).
Vervolgens wordt boven de putkelder een ca. 52 m. hoge boortoren opgebouwd.
Deze toren werd in de zestigerjaren opgebouwd m.b.v. een grote linkbeltkraan.
Augustus 1959. De put Slochteren 1 wordt langdurig onderworpen aan druktetsen. Dit ging gepaard met bulderende fakkels. In de avonduren was destijds de wijde omgeving oranjegeelgekleurd. Dit trok vele toeristen naar de boorlocatie.
Het fakkelen ging dan en nacht onafgebroken door. De test wees al snel uit, dat er sprake kon zijn van een enorm gasreservoir in de ondergrond.
Op onderstaande foto's een aantal boortorens, welke door de NAM werden ingezet voor het boren van ca. 300 putten op het gasveld Groningen.
De PT 105 op de locatie Vierhuizen nabij Zoutkamp. Uitgevoerd met takelblok en draaischijf op boorvloer
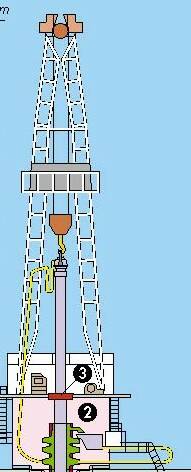
Schematische weergave van de boortoren:
1. Boven in de toren bevindt zich het kroonblok, met grote schijven, waarover dikke staalkabels lopen t.b.v het hijswerk met het takelblok.
2. In de toren hangt het grote en zware takelblok met blokhaak, voor de boorstang en het laten zakken van de bekledingsbuizen van de put.
3. Onder de blokhaak bevindt zich de spoelkop, waaraan de spoelingslang is bevestigd. Daaronder zit tijdens het boren de Kelly- of meeneemstang, waardoor ook de te gebruiken boorspoeling door de boorstang naar de boorbeitel wordt gepompt.
4. Op de boorvloer bevindt zich centraal de draaitafel, die zorgt voor het ronddraaien en aandrijven van de kellystang. Waardoor de gehele boorstang incl. de boorbeitels gaan draaien.
5. Onder de boorvloer, wordt de terugvloeiende boorspoeling met het vrijkomen boorgruis naar de trilzeven gevoerd. Het begruis komt in grote containerbakken en de gezeefde spoeling wordt hergebruikt.
6. Op de boorput staat bovenop de conductor een grote veiligheidsafsluiter (Blow-out preventer). Deze kan bij calamiteiten worden afgesloten en is ook op afstand bedienbaar.
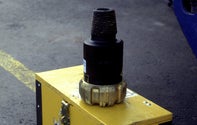
Kleine boorbeitel. voor het diepere boorwerk, waar de put een kleinere diameter heeft.
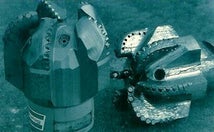
Grote en zware boorbeitels. Tijdens het dieper boren van de put, wordt de diameter van de te gebruiken beitels steeds kleiner.
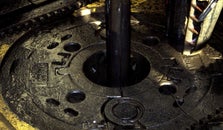
De draaischijf in het hart van de boorvloer, zorgt voor ronddraaien van de boorstang.
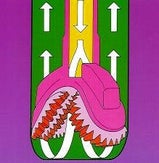
De boerspoeling wordt door de holle boorstang vanuit de toren naar de beitel gepompt. Vervolgens gaat de spoeling langs de boorstang en de wand van het boorgat weer naar boven en neemt gelijk het vrijkomende boorgruis mee naar boven.
De stabiele onderbouw van de toren, met in het midden zichtbaar de veiligheidsafsluiter op de put geplaatst.
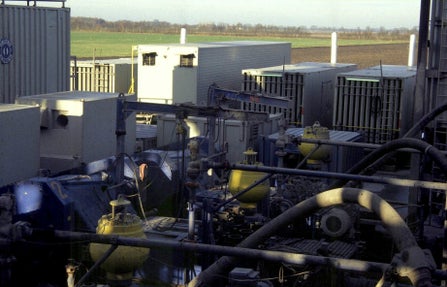
Achter de toren, staan een aantal spoeling (mud pompen) opgesteld, voor de aanvoer van de spoeling. Daarachter staan grote dieselgeneratoren voor energielevering voor aandrijving van het geheel.
Foto links:
Tijdens het wisselen van de boorbeitels, hangen alle omhoog getrokken boorstangen in de toren. Gedurende het boren van de put gebeurt dit verscheidene keren.
Foto rechts:
De topdrive voor aandrijving zoals die in latere jaren werd gebruikt in de modernere boortorens.
De werking van de boortoren:
Om te boren naar olie of aardgas, is het noodzakelijk dat een kleine locatie wordt aangelegd voor het verrichten van een zgn. proefboring, zoals in 1959 gebeurde bij Kolham (gemeente Slochteren).
De draaitafel te vinden in het hart van de boorvloer van de toren zorgt voor de aandrijving van de boorkop. In deze draaitafel loopt de vier- of zeskantige kellystang mee, die weer zorgt voor het draaien van de boorstang, waaronder zich de boorbeitel bevindt.
De holle boorstangen worden telkens als er 1 met een lengte van 9 m is afgedraaid met een nieuw deel verlangt. Door het gewicht van de kolom boorstangen draaien deze de beitel zelf de aarde in. Door het telkens verlengen van de boorstang, wordt het uiteindelijke boorgat steeds dieper.
Tijdens het boren wordt er spoeling (mud) door de boorstang naar de beitel gepompt. Van onderaf gat de spoeling tussen boorstang en boorwand weer naar boven en neemt het vrijkomende boorgruis mee.
Boven op de boorvloer gaat de spoeling met het boorgruis naar schudzeven, waar de spoeling van het boorgruis wordt gescheiden. Het boorgruis wordt vervolgens in containers gestort en afgevoerd. De spoeling wordt hergebruikt.
De vrij zware spoeling zorgt er door haar gewicht tevens voor dat er geen gas of olie kan ontsnappen naar de oppervlakte.
Op het boorgat staan grote veiligheidsafsluiters (Blow out preventer), die tijdens calamiteiten ook op afstand kan worden gesloten.
Tijdens het boren moet worden voorkomen, dat het boorgat kan instorten. Het boren wordt dan ook een aantal keren gestopt, om de put te verbuizen met ruimere stalen bekledingsbuizen (Casing). Met cement worden deze aan de boorwand vastgezet.
Hoe dieper een boorgat wordt zullen meerdere keren casing aangebracht worden. Ook de samenstelling van de gesteentelagen is hiervoor bepalend.
Het boorgat heeft boven een veel ruimere diameter dan onder. Daardoor wordt er telkens per fase geboord met kleinere boorbeitels.
Wanneer de boorbeitel is versleten, of er een kleinere diameter gemonteerd moet worden, haalt men de hele boorstang uit de put naar boven. Deze boorstangen worden ter hoogte van het vingerbordes in de toren gezet.
Aan het begin van de boring, verloopt dit proces vrij snel. Soms kan men in 1e aanzet wel 60 m. per uur boren. Naarmate men dieper in de hardere gesteentelagen komt, boort men in sommige gevallen niet meer dan 20-25 cm per uur.
Er wordt op verschillende manieren onderzocht of er olie of gasdelen worden aangetroffen. De met de boorspoeling naar bovenkomende boorgruis, geeft vaak aan in welke aardlaag de beitel zich bevind.
Ook het regelmatig uitboren van boorkernen uit het gesteente, die in laboratoria worden onderzocht kunnen aanwijzingen geven.
De ontdekkingsplaats in 1959 op het land van boer Boon.
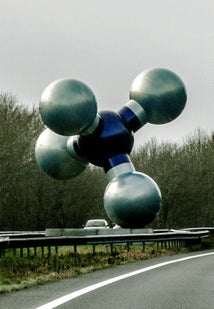
Aardgasmolecuul aan de A7 nabij Hoogezand. Geplaatst in 1909 50 jaar na de ontdekking.
Lang niet elke proefboring is een succes:
Wanneer er geen olie of gas wordt aangetroffen, spreekt men van een droge put. Toch zijn de genomen gesteentemonsters zeer waardevol voor de geologen, voor nader onderzoek van de aardlagen.
Is er wel gas aangetroffen, dan kan alleen het lange tijd testen van de put de omvang en waarde van het reservoir bepalen. Het vrijkomend gas wordt tijdens dit testen afgefakkeld.
Hierna wordt gekeken of de put voor productie rendabel kan zijn.
Het testen gebeurt uit verschillende dieptes in de formatie. Loopt tijdens deze testperiode de druk vrij snel terug dan is er waarschijnlijk sprake van een kleine onrendabel reservoir.
Als tijdens het testen zoals destijds bij de ontdekkingsput Slochteren 1 de druk langere tijd niet daalt, dan zaal er sprake zijn van een goede producent, hetgeen op Slochteren 1 het geval was.
Alvorens er gas in uit de put kan stromen, moet het onderste deel van de zgn. tubingbuizen dat zich in de zandsteenformatie bevind worden geperforeerd.
Hiervoor wordt speciale apparatuur gebruikt.
Perforatie van de casingbuis is een van de meest toegepaste kabelwerkzaamheden die in een verbuisde put worden gedaan.
Om doorstroming van olie of gas uit het reservoir naar de put te verkrijgen, moet de casing worden geperforeerd.
Lange tijd werd met kogels geperforeerd. Deze kogels werden afgevuurd met een soort geweer onder in de put. Na een drietal schoten word de kabel getrokken en bovengronds opnieuw geladen.
Tegenwoordig wordt er op een andere manier geperforeerd. Dit zorgt voor een betere perforatie.
Door middel van explosieve ladingen worden gaten gebrand door de casing door het cement achter de casing
Maak jouw eigen website met JouwWeb